Controlling Flash in Extrusion Blow Molding
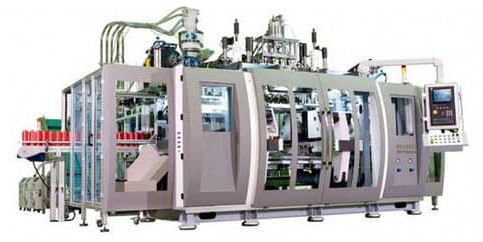
Flash is essentially the rejected waste of the process – and the problem with flash is that it can impose restrictions on the overall efficiency of the blow molding process while leading to an increased reject rate of product. The primary problem with flash is that it can attach itself to the molded part, thereby causing that part to be rejected. This poses problems associated with an increased reject rate of formed parts; leading to a slower manufacturing time with lost time and efficiency. Some of the associated problems can occur include:
-
The flash pocket isn’t large enough to hold the flash material; thereby resulting in too much plastic material;
-
The flash pocket doesn’t fill properly, which can happen if the pressure is inadequate. This will force plastic back to the container;
- If there are any shortcomings with the process geometrics or effectiveness, this will in turn lead to pinch-off problems.
PET ALL MANUFACTURING INC.
85 Royal Crest Court, Units 1 & 2 Markham,
Ontario, L3R 9X5
Phone: (905) 305-1797
Email: cmerrick@petallmfg.com