Stretch Blow Molding: Advantages of Stretching Your Containers
Unlike injection blow molding that is used to create very small containers, stretch blow molding is commonly used for making soda bottles, personal care containers, household cleaner containers, and so on. Depending on what the customer wants, extrusion blow molding products are made. If the final product will consist of plastic, then plastic blow molding is the correct process. Regardless of the material, container, or part created, it is imperative to rely on a high-quality blow molding machine.
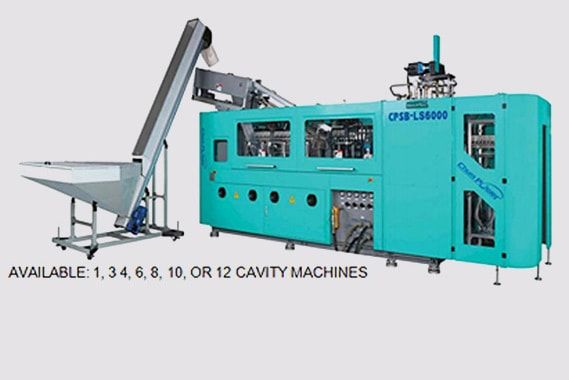
There are several benefits to the injection stretch blow molding process. While learning about those, you will also gain insight into the blow molding process, step by step. With this molding process, PET bottles used for soda, water, juice, package detergent, and various other products are made. Depending on which type of stretch blow molding is used, single-stage or two-stage, the advantages differ slightly.
With the single-state process, an extruder injects parison into a fast-cooling preform mold. This preform is then reheated and placed into the container mold. Because the parison is hot and soft, its original length can actually be doubled. Once stretched, high-pressure air fills the container, which is then stretched to fit the mold. It remains in place until completely cooled and hardened. This single-stage stretch molding process is beneficial for producing jars with wide mouths when a high production rate is not required.
Read more at the original source:
http://www.petallmfg.com/blog/stretch-blow-molding-advantages-of-stretching-your-containers/
Contact Details:
PET ALL MANUFACTURING INC.
85 Royal Crest Court, Units 1 & 2 Markham,
Ontario, L3R 9X5
Phone: (905) 305-1797
Email: cmerrick@petallmfg.com
85 Royal Crest Court, Units 1 & 2 Markham,
Ontario, L3R 9X5
Phone: (905) 305-1797
Email: cmerrick@petallmfg.com