Stretch Blow Molding and Its Various Uses
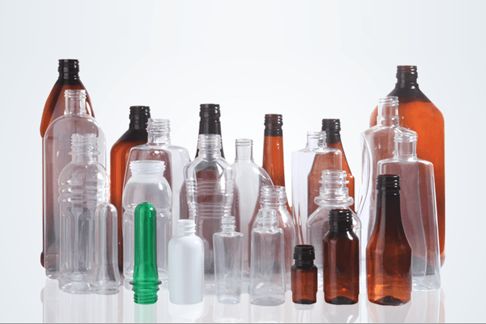
Although stretch blow molding produces a
variety of products, it is best known for the production of PET bottles
used for juices, sports drinks, water, and similar products. First
introduced in the early part of the 1970s thanks to advanced materials
and techniques, it is now what manufactures prefer among the different
types of blow molding for making bottles for carbonated beverages.
The primary
benefit of using this molding process is that it can stretch a preform
in both the axial and hoop direction. With the biaxial stretching of
materials, tensile strength increases, as does clarity, drop impact,
barrier properties, and top load. Also, the weight of the container
decreases by as much as 15 percent compared to using one of the other
types of blow molding processes.
There are two categories: single-stage
and two-stage. For the single-stage, an extruder injects a parison into
the preform mold where the plastic material cools rapidly to form the
preform. Once reheated and placed into the bottle mold, the now-softened
parison stretches to roughly 50 percent of its original length. At that
point, compressed air gets blown into the parison, expanding it to the
bottle mold. After the bottle cools, the mold opens and the finished
product ejects.
Read full post at the original source: http://www.petallmfg.com/blog/stretch-blow-molding-and-its-various-uses/
Contact Details:
PET ALL MANUFACTURING INC.
85 Royal Crest Court, Units 1 & 2 Markham,
Ontario, L3R 9X5
Phone: (905) 305-1797
Email: cmerrick@petallmfg.com
PET ALL MANUFACTURING INC.
85 Royal Crest Court, Units 1 & 2 Markham,
Ontario, L3R 9X5
Phone: (905) 305-1797
Email: cmerrick@petallmfg.com
.