Stretch Blow Molding Machinery for Plastic Bottles
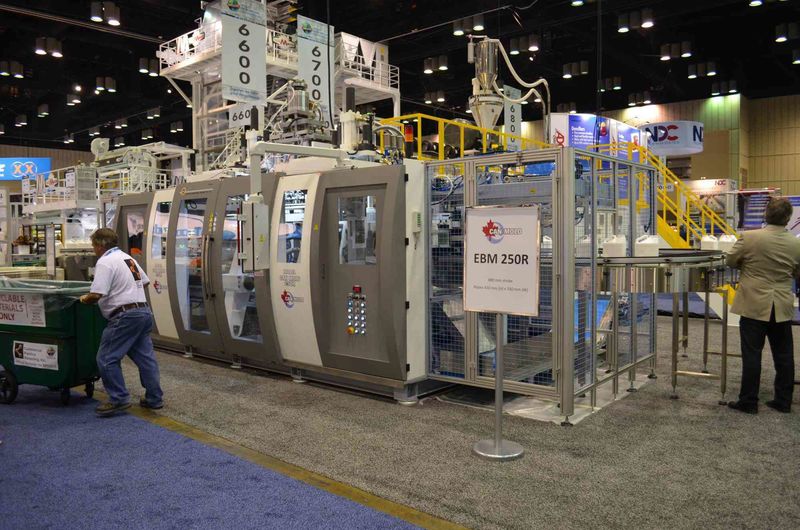
Blow Molding Process Step by Step
Using the appropriate blow molding equipment, a tube of molten plastic is created, followed by it being inflated into the shape required by the customer. With the injection stretch blow molding process, a part with a bi-axial molecular alignment is produced. In this case, a preform is elongated via a mechanical process in a mold. Next, the preform is significantly expanded during the blowing process. Compared to the other blow molding methods, the stretch process uses a lower temperature to achieve the required molecular orientation. This makes it somewhat more challenging.
Once the molecular orientation is achieved, the material is extremely strong. A huge advantage of the injection stretch blow molding process for plastic bottles is that less material is required compared to other molding processes. Although various types of bottles are produced with this method, it is most commonly used for manufacturing PET bottles.
PET ALL MANUFACTURING INC.
85 Royal Crest Court, Units 1 & 2 Markham,
Ontario, L3R 9X5
Phone: (905) 305-1797